Before we begin, this “How to use a Plasma Cutter” guide is to help equip you with the best and safe practices to become an effective metal forger, knowing not only the skills but also the physics and chemical reactions throughout the process.
Metal fabrication can be fun to work but also involves risk therefore in this guide, we will help point out some basic features to look for when purchasing a plasma cutter to insure you get a machine that you will be happy with in the long run. Besides, we will walk you making your first cut safely..
Our step-by-step plasma cutter guide will help you to increase your efficiency, prolong the life of your equipment and improve your cut quality.
Contents
- 1 Plasma Cutting – An Overview
- 2 What Is A Plasma Cutter?
- 3 What are a couple of benefits to using a plasma arc cutter?
- 4 What should I look for when buying a plasma cutter?
- 5 Extra tools for Plasma Cutter.
- 6 How do you use a plasma cutter safety?
- 7 How Do I Cut With A Plasma Cutter?
- 8 How to use a Plasma Cutter: Plasma Cutting Operation
- 9 Concluding Thoughts
Plasma Cutting – An Overview
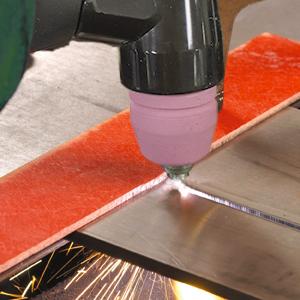
Metal cutting requires a precise, dross-free finish to make the desired product. The cutting process with superior material interaction should be clutter-free, and less time-consuming. Plasma cutters offer remarkable results emerging as an alternative over traditional cutting processes. The process requires compressed air and electricity to produce the plasma arc. The machine assembly is less complicated, requiring no additional tools.
The learning curve is the usual ritual starting from the basics and improvising. The plasma cutter’s ease of use enables high quality and high volume production in a shorter time. Considering its dominant role, plasma metal cutting skills can enhance your career prospects.
What Is A Plasma Cutter?

Adding heat/energy to compressed air or gas produces “Plasma”. This ionized state is also called the “fourth state of matter” penetrating through metals. Plasma cutters focus the ionized gas on the metal region weakening the atomic bond. The metal dissects because of the concentrated discharge of ionized gas. The plasma gun uses a combination of nozzle-air pressure mechanisms to control the arc.
One example to understand the process is “Lightning”. The electrical charges emitted by lightning ionizes the gas present in the air. The conductive rays manifest in the form of light and electrical charge. The Plasma cutter as a tool is fairly portable, consisting of simple mechanical units that mimic a normal weld gun.
What are a couple of benefits to using a plasma arc cutter?
Plasma cutting can improve productivity and lower the cost of cutting. Benefits of plasma cutting include:
- Faster cuts
- No pre-heat cycle required
- Cuts any metal that conducts electricity (unlike oxy-fuel, which cannot cut stainless steel or aluminum)
- Offers portability around jobsites
- Minimizes the heat-affected zone and yields a cut with a small kerf (cut width).
- Plasma units can also gouge, pierce, bevel, cut holes and trace shapes.
Read More: How To Make Metal art – Plasma Cutter Metal Art For Beginners
What should I look for when buying a plasma cutter?
The actual process of operating a hand-held air plasma cutter is relatively simple. In fact, the hardest part comes before ever striking an arc — selecting a machine that best matches your application and choosing the right accessories.
The Thickness of the Material
The thickness of metal you will routinely cut and maximum metal thickness are important in selecting the right plasma cutter.
Most of the time, you should consider choosing a tool that has more than 80% cut-capacity, especially when you are using a handled machine. It is possible to find plasma cutters that can fail to cut a particular thickness, especially when the cutting capacity falls below 75%.
Cutting Quality
Cut quality is one of the most critical factors that you should consider every time you are buying a plasma cutter. Quality cutting has a significant impact on the quality of the finished product while at the same time impacting later stages of production. The smooth and clean cutting means that there is a narrower cut width, which means that there is less wasted material.
Primary power
Plasma cutting requires two basic elements — air and electricity — so the next question to ask is what type of input power is available. If your input circuit has a 30-amp breaker, you even get equal cutting capacity at both voltages (with a 20-amp breaker, cutting capacity drops by 20 percent). If you’re working in the field and plan to use an engine drive’s auxiliary power, strongly consider a plasma cutter with Auto-Line technology. Similar units without Auto-Line experience erratic cutting arcs, frequent breaker trips, blown circuit boards and are prone to premature transformer failure. These problems typically occur because the plasma cutter, once triggered, places such a load on the line that voltage levels drop below the plasma cutter’s operating range.
Environment and air supply
In environments with heavy dust and metal shavings (such as from grinding). With Wind Tunnel Technology, the cooling air flows through the machine without blowing over the electronic components, so grinding dust can’t settle on critical components. Fan-On-Demand means the cooling fan runs only when needed, reducing the amount of debris entering the unit. Regarding air supply, most manufacturers of hand-held plasma cutters recommend using ordinary air as the cutting gas. In mobile applications, contractors often opt for bottled nitrogen because it costs less than bottled air. When cutting stainless steel, some people believe nitrogen produces slightly less oxidation, as it is drier than compressed air.
High frequency starts or contact starts
Plasma cutters use either high frequency (HF) start or contact start technology to initiate the pilot arc. If you plan to use a plasma cutter near telephones, computers, CNC machines or other electronic equipment, be aware that HF often interferes with electronic controls. The contact start method also creates a visible pilot arc that helps you better position the torch.
Reliability
Reliability is another important consideration when you are purchasing plasma cutters. You should make sure that an ISO certified company manufactures your cutting system and that it meets the ISO standards. A reliable machine can easily be detected because it uses more software than hardware. Heating is a critical aspect of the cutting machine, which means that you should consider plasma cutting machines that have an effective cooling system. For example, a centralized fan that will help in bringing the air through the central system where heat-sensitive equipment is located. Continuous cooling will enable the system to perform excellently and higher reliability.
Ease of Use
It is common knowledge that one plasma cutting machine can be easy to use as compared to another one of a similar category. Ease of use allows the operator to perform the work efficiently and use the minimum time possible to perform a particular task. People with minimum experience can also be able to work with an efficient machine and get good results. You should make sure that you purchase a machine that can be used by any person, regardless of experience. Taking a long time to complete a particular task can be considered as a loss to an organization that is working towards a specific objective.
Size & Weight
Size and weight are important factors that should be considered, especially by individuals who tend to move a lot in their workshop. Recent advancement in technology has allowed individuals to get a quality plasma cutting machine that is lightweight without sacrificing power and performance. A lightweight plasma machine can easily be carried from one corner of the workshop to the other. It is also clear that you can get a plasma cutter that can automatically adjust voltage, which is an important aspect, especially if you are planning to use a generator.
Read More: 10 Best Plasma Cutters: Complete Buying Guide and Review 2021
Extra tools for Plasma Cutter.
Adding tools makes a huge difference in the fabrication process. The assembly provides an economic alternative to automation and CNC.
Fume control mechanism
Field use or bulk fabrication projects may involve smoke or fumes. Downdraft or water table fume can control fumes. The control system must be effective in capturing particles of all sizes. They come in two different types;
- Water Table
The water table control uses water both as a coolant and to attract the particles. The base metal mounts over the water table allowing the bed to arrest particles. The water table acts as a coolant, besides, so preferred in some processes.
- Downdraft Table
The Downdraft table uses a power air control mechanism to drive off the particles through a duct. This method is effective in metal cutting operations generating large particles.
Mechanical tools
The Integration of different mechanical components is based on production size. The industrial set-up has precise and heavy-duty peripherals with robust mechanisms. Peripherals are a good economic investment in entry-level metal cutting operations.
Stepper motors offer an easy alternative in operations involving lightweight machines. They can give precise and repetitive movements that can increase production volume. Servo motors are used in advanced cutting processes. It requires software back-end and coding skills.
Plasma cutting table
A cutting table locks the base material avoiding splinters from falling on the floor. Ensuring a rigid and ergonomic cutting table optimizes the workplace for better productivity.
Magnetic guide
Let’s accept that metal cutting maneuvers around curves can be challenging. Cutting the metal with precision and reduction of waste is crucial. Magnetic guides help maneuver the torch as per the design. This makes dealing with complicated curves and arcs easier.
Read More: 5 Welding Safety Tips That Every Welder Should Know
How do you use a plasma cutter safety?
Protective Clothing
When it comes to working with a plasma cutter it is important to know that this machine can cause serious injury if used incorrectly. However, with basic safety gear and safety rules a plasma cutter is a safe tool to use.
Here is some the safety gear we recommend
- Plasma Helmet for eye and face protection
- Welding beanie to protect your hair from sparks
- Welding jacket to protect your arms and torso
- Welding gloves to protect your hands
- Set of jeans to protect your legs (welding leathers to cover your legs is also a great idea)
- Laced and tied boots to protect your feet from both sparks and dropping pieces of metal (we recommend steel toe that are laced tight to prevent any metal from dropping inside of your boot).
- Fire extinguisher
Safety Equipment
Here are some final steps before you start cutting:
- Follow proper safety procedures and wear personal safety equipment. Always read the Owner’s Manual.
- Inspect the torch tip, electrode, and shield cup and replace worn items. The expense is well worth avoiding the poor cutting performance (and operator frustration) caused by worn parts.
- Check gas/air pressure at the compressor or bottle gauge.
- After turning on the plasma cutter, set the amperage control (generally to maximum) and check the air pressure.
- Grind off rust or paint where you plan to secure the ground clamp.
- Place the ground clamp as close to the cut as possible, and place the clamp on the workpiece itself when possible. Check for any loose connections between the work cable and the clamp.
- Relax your hand and don’t hold the torch too firmly, as this will make your hand shake more.
Read More: Get familiar with how to use a CNC Plasma Cutter
How Do I Cut With A Plasma Cutter?
Our step-by-step plasma cutter guide will help you to increase your efficiency, prolong the life of your equipment and improve your cut quality.
1 – Make Sure The Working Area Is Clean: Before setting up the plasma cutter to start cutting, make sure that the working environment is as clean as possible. If there is dust or grinding debris around the unit, the cooling fan may suck these particles and it can cause serious damage to the unit. Ensure you are wearing the appropriate plasma cutting safety gear as well.
2 – Set Up Stable Work Surface: The working surface needs to be safe. Working with a plasma cutter can be risky if you place and work on a surface that isn’t stable. If you place the metal on a surface that works like a table, make sure that the setup is strong enough to cut on. Using a metal clamp to hold the piece down makes the cutting procedure secure.
3 – Plug-In The Plasma Cutter:Make sure that the device is power off and plug it in.
4 – Connect the Air compressor: If the plasma cutter doesn’t feature built-in air compressor, connect the external air compressor to the unit. A gas such as compressed air is a requirement for the plasma cutter to function.
5 – Turn on your air compressor and start building air pressure: At this step, turn the air compressor on.
6 – Attach The Ground Clamp: Get you metal positioned in a vice, on sawhorses, or clamped to a table.
7 – Turn On The Machine: Generally, you’ll find the on-off switch behind the unit. Turn on the plasma cutter by flipping this switch into the ON position.
8 – Set The Amperage: Set the amperage control. You can try different amps depending on how thick the metal is that you are cutting.
9 – Cut The Metal: Keep the nozzle end on the edge of the base metal. Push the trigger to start the arc. Slowly move the torch over the metal. If you have any plasma templates, use the guide surrounding the nozzle.
10 – Switch Off The Machine: When you’re done turn off the unit.
11 – Disconnect The Ground Clamp: Don’t forget to disconnect the clamp from the metal.
12 – Turn Off Air: At this stage, by rotating the lever 90 degrees, turn off the air.
13 – Let The Torch To Cool And Wind Up All Hoses: You’ve just finished your cutting job, let the torch to cool. After releasing the trigger, post-flow air lasts for 20-30 seconds. Wind up all hoses and wrap up the torch, airline, and ground line.
How to use a Plasma Cutter: Plasma Cutting Operation
Now that you’ve selected your plasma cutter and completed your pre-cut checklist, here’s how to get started plasma cutting:
- Step 1: Place the drag shield on the edge of the base metal or hold the correct standoff distance (typically 1/8 inch) and direct the arc straight down.
- Step 2 : Raise the trigger lock and press the trigger — and pilot arc starts immediately when the trigger is pressed.
- Step 3:Once the cutting arc starts, begin to slowly move the torch across the metal.
- Step 4: Adjust your speed so sparks go through the base metal and out the bottom of the cut.
- Step 5: At the end of the cut, angle the torch slightly toward the final edge or pause briefly before releasing the trigger to completely sever the metal.
- Step 6 :To cool the torch, post-flow air continues for 20 to 30 seconds after you release the trigger. Pressing the trigger during post-flow instantly restarts the arc.
Concluding Thoughts
I hope this guide helped you in your metal engineering and fabrication endeavors. There’s always excitement surrounding a new tool. This guide is a small attempt in understanding plasma cutting technology. It has an amazing scope in metal fabrication saving a lot of time and resources. I hope you enjoyed reading this guide, best wishes for your endeavors, and thanks for reading.
Making the switch to plasma cutting can deliver great results. If you select the appropriate plasma cutter and service it properly, you can experience years of trouble-free performance.
Read More: How To Make A DIY Plasma Cutter At Your Home?
References:
https://plasmacutteradvisor.com/how-to-use-a-plasma-cutter/
https://www.millerwelds.com/resources/article-library/how-to-select-and-operate-a-hand-held-plasma-cutter
https://primeweld.com/blogs/news/how-to-choose-the-right-plasma-cutting-machines